Understanding Lean and Six Sigma in Life Sciences – A Practical Guide
Introduction
In the life sciences industry, where precision, efficiency, and compliance are the cornerstones of success, navigating operational complexities is more challenging than ever. This sector operates under the pressure of strict regulations, high research and development (R&D) costs, and the demand for consistent, high-quality products. Achieving these objectives while remaining competitive requires robust strategies that drive continuous improvement and optimization. This is where Lean and Six Sigma methodologies come into play.
Lean and Six Sigma have proven to be transformative for industries worldwide, but their relevance in life sciences is particularly significant. These methodologies provide a structured framework to streamline operations, reduce waste, minimize process variability, and ensure quality, all of which are vital for regulatory compliance and operational success. By adopting Lean and Six Sigma, you can not only meet the high standards of the industry but also enhance your processes and contribute to organizational efficiency.
This guide explores the fundamental concepts of Lean and Six Sigma, their critical relevance to the life sciences sector, and practical ways to implement these methodologies. Whether you work in pharmaceuticals, biotechnology, or medical devices, understanding how to integrate Lean and Six Sigma into your processes can be a game-changer, driving both immediate improvements and long-term gains.
What Are Lean and Six Sigma?
Lean and Six Sigma are two powerful methodologies for driving Operational Excellence (OpEx). Here’s a quick overview of each.
- Lean: Lean focuses on eliminating waste and enhancing flow in processes, ensuring that every step adds value. Key Lean tools, such as Value Stream Mapping (VSM) and Kaizen, help identify inefficiencies and streamline workflows.
- Six Sigma: Six Sigma is a data-driven methodology aimed at reducing variability and improving quality by eliminating defects. Its core framework, DMAIC (Define, Measure, Analyze, Improve, Control), provides a structured approach to problem-solving and process improvement.
When combined, Lean and Six Sigma offer a comprehensive approach to refining processes, cutting costs, and maintaining compliance in the life sciences.
Why Lean and Six Sigma Matter in Life Sciences
1. Compliance and Quality Control
Lean and Six Sigma are essential for navigating the complexities of regulatory requirements. These methodologies help build quality directly into processes, ensuring consistency, reducing errors, and maintaining compliance with guidelines set by regulatory bodies like the FDA and EMA. Applying Lean and Six Sigma enhances operational efficiency and reliability, making it easier to meet the rigorous standards that govern the industry.
2. Increased Efficiency and Cost Reduction
Lean and Six Sigma are invaluable in identifying and eliminating non-value-added activities, enabling better resource utilization and reduced operational costs. This is particularly critical in life sciences, where high R&D expenses and stringent regulatory demands are a constant challenge. Streamlined processes that focus on value-added steps allow organizations to improve efficiency and remain competitive in a complex landscape.
3. Enhanced Product Quality and Patient Safety
Consistency in product quality is vital in life sciences, as even minor variations can impact patient safety. Six Sigma tools help reduce process variability, ensuring that every product meets stringent quality standards. This focus on consistency supports the integrity of the final product, protecting patient safety and reinforcing trust in the organization’s work.
Key Lean Tools
1. Value Stream Mapping (VSM)
VSM helps visualize the entire process flow from start to finish, allowing teams to see where value is added and identify inefficiencies. For instance, mapping out a pharmaceutical testing process might highlight delays between stages that can be streamlined. The result is improved workflow, reduced lead times, and better resource allocation, ensuring resources are focused where they’re needed most.
2. Kaizen
Kaizen emphasizes continuous, incremental improvements through teamwork and active participation. Regular Kaizen events bring cross-functional teams together to brainstorm, test, and implement improvements. For example, a biopharma team might use Kaizen to optimize equipment changeovers. This tool fosters a culture of innovation and engagement, resulting in greater productivity and ongoing process enhancements.
3. 5S System
5S promotes workplace organization through Sort, Set in Order, Shine, Standardize, and Sustain principles. Applying 5S in lab spaces or manufacturing floors creates a more efficient, organized environment, reducing time spent searching for tools and minimizing clutter. This leads to safer, more productive workspaces that enhance quality control and workflow.
Key Six Sigma Tools
1. DMAIC Framework
DMAIC is a structured problem-solving process that helps teams address specific quality issues systematically. Use DMAIC to tackle issues like reducing variability in drug production. Start by Defining the problem, Measuring current performance, Analyzing root causes, Improving the process, and Controlling the solution to maintain gains. DMAIC leads to fewer defects, greater process control, and more consistent quality. By systematically identifying and addressing root causes, it helps optimize processes, ensuring that each output meets the desired standards with less variation and higher reliability.
2. Root Cause Analysis (RCA)
RCA is used to identify the underlying causes of defects or quality issues, enabling teams to address problems at the source. RCA methods, like the 5 Whys or Fishbone Diagram, to dig deep into recurring issues, such as contamination in lab samples. By understanding the root cause, you can implement targeted solutions. Root Cause Analysis (RCA) helps eliminate recurring issues and builds a stronger foundation for quality assurance. Identifying and addressing the underlying causes of problems ensures more sustainable solutions, reducing future disruptions and improving overall process reliability.
3. Statistical Process Control (SPC)
SPC uses statistical methods to monitor and control processes, helping teams identify when a process is out of control before issues escalate. Use SPC to track critical quality attributes (CQAs) in a production process, plotting data on control charts to detect trends or deviations. This helps maintain process stability and compliance. Statistical Process Control (SPC) enables early detection of variability, allowing for timely adjustments that help maintain consistent quality standards. By continuously monitoring processes, SPC ensures that deviations are addressed before they impact the final product, ensuring reliability and minimizing waste.
Steps to Implement Lean and Six Sigma
Identify Opportunities for Improvement
Start by analyzing current workflows to identify bottlenecks, waste, or variability that impact quality, cost, or speed. For example, are there delays between testing stages in your lab process? Or is there excessive time spent on manual data entry?
Step 1. Set Specific Goals and Metrics
Define measurable objectives for your OpEx initiative. For instance, aim to reduce batch processing time by 20% or decrease error rates in documentation. These goals will help you track progress and prove the value of your improvements.
Step 2. Utilize a Structured Framework
Follow DMAIC to address specific challenges or conduct regular Kaizen events to encourage incremental changes. Document each stage of your progress, which is especially important in regulated environments.
Step 3. Leverage Cross-Functional Collaboration
Lean and Six Sigma thrive on collaboration. Involve colleagues from different departments, such as quality, production, and compliance, to gain diverse perspectives and address potential impact areas holistically.
Step 4. Monitor, Measure, and Adjust
Use tools like SPC and control charts to monitor improvements over time. This not only helps maintain gains but also demonstrates the effectiveness of your efforts to stakeholders and regulators.
Conclusion
Lean and Six Sigma provide a powerful framework for achieving Operational Excellence, merging quality, efficiency, and compliance seamlessly. By integrating these methodologies into day-to-day operations, you create a culture of continuous improvement. The long-term advantages of Lean and Six Sigma include more robust processes, higher-quality outcomes, and enhanced operational agility.
Now is the time to take action. Whether you start with Value Stream Mapping, host a Kaizen event, or apply the DMAIC process, incorporating Lean and Six Sigma into your workflow positions you for success. In an industry where stakes are high and competition is fierce, these tools are not just beneficial; they are indispensable. Embrace Lean and Six Sigma to drive meaningful change.
Want to learn more about Operational Excellence (OpEx) in the Life Sciences industry?
Follow us on LinkedIn and Download PharmAllies’ White Paper on Operational Excellence (OpEx) in the Life Sciences Industry.
Download the White Paper HERE
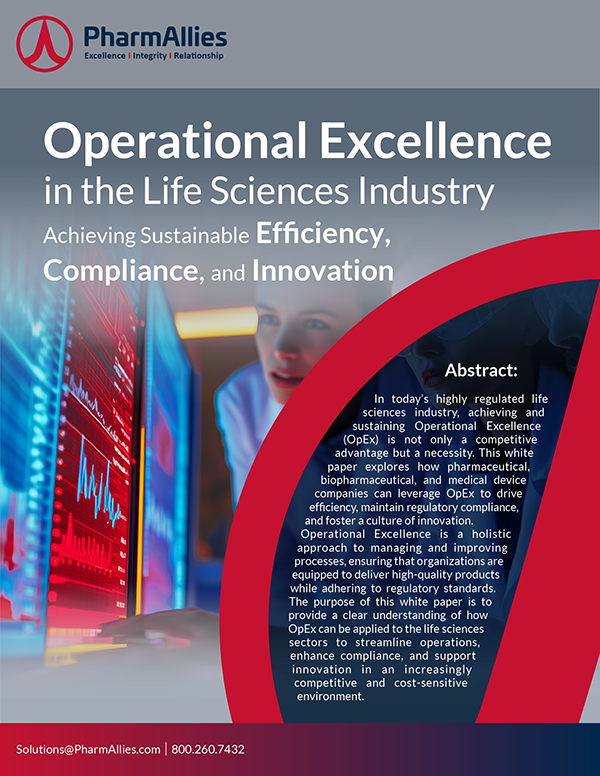
Discover how Operational Excellence drives efficiency, compliance, and innovation in life sciences with PharmAllies’ latest white paper.