The Holistic Journey of Commissioning, Qualification, and Validation (CQV)
Introduction
Throughout my career in the life sciences industry, I’ve come to appreciate the immense value of a comprehensive and interconnected approach to Commissioning, Qualification, and Validation (CQV). Having worked on numerous projects over the years, I’ve seen firsthand how the seamless integration of these phases can make or break a project. It’s not just about ticking boxes to satisfy regulatory requirements—although that is unquestionably crucial—but about laying a foundation for long-term operational excellence.
The life sciences industry is one of the most regulated sectors, and for good reason. We’re responsible for ensuring that products are safe, effective, and of the highest quality. This responsibility is reflected in the processes we follow, from the initial design and installation of equipment to the final validation of a system’s performance. But what I’ve learned through years of experience is that these processes are most effective when viewed as an interconnected journey rather than isolated steps. By integrating Commissioning, Qualification, and Validation into a cohesive process, we can not only meet regulatory standards but also create a more efficient, reliable, and successful project outcome.
Setting the Stage with Commissioning
Commissioning is where the journey begins. It’s the critical first step that sets the tone for everything that follows. This phase involves a thorough evaluation of design intentions to ensure that systems are installed correctly and are operationally fit for their intended use. In my experience, this stage is often underestimated, but it’s absolutely pivotal. A robust commissioning process can catch potential issues before they become significant problems, saving time, money, and resources down the line.
During commissioning, I take a meticulous approach, focusing on several critical activities that ensure everything is set up correctly from the start. This includes a comprehensive review of design documentation, thorough installation checks, initial operational testing, and detailed documentation of all activities. These steps are essential for establishing a solid foundation, not just for the qualification phase but for the entire lifecycle of the system. When done right, commissioning can significantly reduce the risk of issues arising later in the project, paving the way for a smoother qualification and validation process.
Refining Through Qualification
Once commissioning is complete, the focus shifts to Qualification. This phase is all about verifying that the systems and equipment installed during commissioning perform reliably within specified limits under simulated production conditions. Qualification is typically broken down into Installation Qualification (IQ), Operational Qualification (OQ), and, in some cases, Performance Qualification (PQ).
In my approach, I ensure that each of these segments builds on the commissioning groundwork with enhanced specificity and attention to detail. During IQ, we verify that everything is installed correctly according to design and specifications. OQ involves testing the equipment under various operational conditions to ensure it functions within the required parameters. Finally, PQ, if applicable, confirms that the equipment can consistently produce outputs that meet predetermined criteria under actual production conditions.
This structured approach to qualification not only ensures compliance but also enhances the system’s reliability and quality. By meticulously refining each step, we can identify and address potential issues before they escalate, ensuring that the system is ready to perform as expected in a real-world environment.
Concluding with Validation
Validation is the culmination of the CQV journey. It provides the conclusive evidence that the systems, when operated as intended, consistently produce results that meet all predefined specifications. This phase is crucial for demonstrating compliance with regulatory requirements and ensuring the safety and efficacy of the products being manufactured.
I’ve always viewed Validation not as a standalone activity but as a natural extension of the work done during commissioning and qualification. Our validation processes are designed to be robust, incorporating risk-based approaches that prioritize and address potential variabilities in system performance. This holistic perspective ensures that by the time we reach the validation stage, most potential surprises have been mitigated. The result is a smoother, more reliable confirmation of system and product integrity.
Validation activities are diverse and tailored to the specific needs of the project. They might include process validation, cleaning validation, computer system validation (CSV), and analytical method validation. Each of these activities is designed to ensure that every aspect of the system meets the stringent regulatory and operational requirements. By taking a comprehensive approach to validation, we can provide the necessary assurances that the system will perform as intended, every time.
The Power of Interconnectedness in CQV
The interconnectedness of CQV is more than just a procedural necessity; it’s a strategic advantage. By understanding and implementing these phases as a continuous process, you can unlock several significant benefits that go beyond mere compliance.
First, this interconnected approach allows for the early identification of potential issues. By addressing problems during commissioning and qualification, you reduce the risk of significant challenges during validation or post-market activities. This proactive approach not only saves time and resources but also enhances the overall quality and reliability of the system.
Second, a seamless flow from commissioning through validation ensures that your project maintains high-quality standards throughout. This is essential in the life sciences industry, where patient safety and product efficacy are paramount. By maintaining these standards, you can ensure that your products not only meet regulatory guidelines but also excel in the marketplace.
Third, integrating CQV into a cohesive process improves operational efficiency. Streamlined processes reduce delays and costs associated with rework or regulatory remediation, leading to more effective project execution and faster time-to-market. This is particularly important in the highly competitive life sciences field, where speed and efficiency can provide a critical edge.
Finally, when CQV phases are well-integrated, the entire project lifecycle can be accelerated. This allows you to bring products to market faster, which is not only beneficial for your business but also for the patients who rely on your products.
Conclusion
As I reflect on my journey through the life sciences industry, I am reminded of the countless projects where the interconnectedness of Commissioning, Qualification, and Validation made all the difference. The holistic approach to CQV is more than just a regulatory requirement; it’s a pathway to achieving operational excellence and setting new standards in the industry.
In the world of life sciences, the journey from commissioning through validation is not just about meeting requirements—it’s about striving for excellence in every aspect of the process. It’s about ensuring that every system, every piece of equipment, and every product is not only compliant but also of the highest quality and reliability. This commitment to excellence is what drives me, and it’s what I bring to every project I undertake.
If you’re looking to refine your approach to project development or enhance your CQV processes, I encourage you to embrace this interconnected journey. It’s not just beneficial; it’s essential for sustained success and leadership in our industry. By investing in a comprehensive and interconnected CQV strategy, you can ensure compliance, drive innovation, improve product quality, and accelerate time-to-market.
Let’s continue to push the boundaries of what’s possible in the life sciences industry. Together, we can create systems and products that set new standards of excellence, reliability, and safety—one project at a time.
Download and Read the White Paper
Download this White Paper to unlock success in your life science projects by integrating Quality Risk Management (QRM) into Commissioning, Qualification, and Validation (CQV) processes. Discover actionable steps for robust project outcomes and embrace a culture of risk excellence. Learn how PharmAllies can help you achieve your quality and risk management goals today.
Download HERE
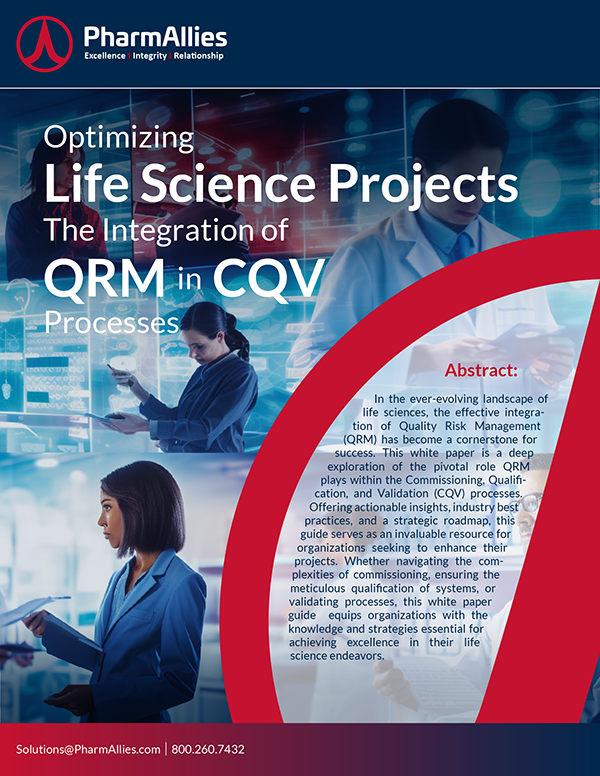
Unlock success in Commissioning, Qualification, and Validation (CQV) projects with our guide. Discover 10 strategic steps for effective Quality Risk Management (QRM).