Mastering 10 Key Quality Risk Management Tools
Embarking on the complex journey of quality risk management tools (QRM) demands understanding risks and the tools that guide this effort. Quality Risk Management Tools (QRM) stand as the guiding compass in this process, ensuring not only quality compliance but the elevation of standards in every aspect. In this exploration, we unveil the significance of 10 key QRM tools, each a strategic asset in fostering excellence and resilience.
From the preemptive insights of the Risk Identification Matrix to the particular analysis enabled by the Audit Trail Review Template, these tools combine into a robust framework. It’s not just about adherence to regulations; it’s a collective effort fortifying the essence of quality and proactive risk management. Instead of drowning you in complex explanations, this article takes a simple approach, providing basic definitions of these ten key QRM tools, along with real-world examples of their application in the Life Sciences Industry.
Risk Identification Matrix
A Risk Identification Matrix is a visual tool that categorizes and prioritizes risks based on their impact and likelihood. It assists in focusing resources on high-priority risks requiring immediate attention.
Example:
Within a biopharmaceutical project, the Risk Identification Matrix highlights a risk associated with a complex supply chain for a critical raw material. The impact is assessed as severe due to potential production delays, and the likelihood is deemed high. This risk is categorized as a top priority, prompting the team to diversify suppliers, maintain strategic inventory, and establish clear communication channels to address potential disruptions swiftly.
Failure Mode and Effects Analysis (FMEA)
FMEA is a systematic method for evaluating processes to identify potential failure modes, their causes and effects, and prioritizing them based on risk.
Example:
Let’s consider the manufacturing process of a pharmaceutical company. In the FMEA process, the team identifies a potential failure mode as a deviation in the mixing step due to equipment malfunction. The causes may include equipment wear or calibration issues. The effects could range from reduced product quality to potential regulatory non-compliance. The team can prioritize this failure mode for corrective action by assigning severity, occurrence, and detection ratings.
Another example:
In the development of a novel medical device, the FMEA process identifies a potential failure mode related to software integration. The cause is determined to be insufficient compatibility testing. The effects range from malfunctions to compromised patient safety. Prioritizing this failure mode, the team implements rigorous compatibility testing protocols, ensuring seamless software integration and mitigating potential risks before the product reaches the market.
Hazard Analysis and Critical Control Points (HACCP)
HACCP identifies and manages potential hazards in processes, crucial for ensuring product safety. This preventive system focuses on identifying critical control points in the production process where hazards can be prevented, eliminated, or reduced to acceptable levels.
Example:
In pharmaceutical manufacturing, the HACCP team identifies a hazard related to cross-contamination during the filling process. Critical control points, such as equipment cleaning and personnel training, are established to prevent or mitigate this hazard. Regular monitoring ensures the effectiveness of these controls, contributing to overall product safety.
Risk Assessment Report Template
The Risk Assessment Report Template provides a structured format for documenting the outcomes of comprehensive risk assessments, aiding in transparent communication and mitigation planning.
Example:
After a thorough risk assessment for a new medical device, the team uses the Risk Assessment Report Template to document identified risks, such as design uncertainties and supply chain disruptions. The report outlines the potential impact on project timelines, patient safety, and mitigation strategies like additional testing and dual sourcing of critical components.
In a pharmaceutical research project:
The Risk Assessment Report Template is utilized to evaluate the potential risks associated with a novel manufacturing process. The template guides the team in systematically documenting identified risks, assessing their impact and likelihood, and proposing mitigation strategies. This comprehensive report becomes a crucial document in discussions with regulatory authorities, demonstrating the proactive approach taken to address potential challenges.
Root Cause Analysis (RCA) Template
RCA systematically investigates the underlying causes of problems, ensuring a focus on addressing root causes rather than symptoms.
Example:
Following a pharmaceutical production batch deviation. The RCA team uses the template to identify the root cause, such as equipment malfunction. Instead of merely addressing the immediate issue. The team implements corrective actions like equipment maintenance and establishes preventive measures to avoid similar incidents in the future.
In a production IT environment
A system outage prompts the use of the RCA Template to investigate the root cause. The template aids in systematically analyzing the incident and identifying contributing factors like software glitches and inadequate backup procedures. By addressing these root causes, the IT team implements preventive measures, enhancing system resilience and minimizing downtime in future scenarios.
Mitigation Action Plan Template
The Mitigation Action Plan Template provides a structured format for outlining actions to reduce or eliminate the impact of identified risks.
Example:
In a clinical trial, the team identifies a risk related to patient recruitment challenges. Using the Mitigation Action Plan Template, they outline actions such as expanding recruitment channels and collaborating with additional clinical sites. This template serves as a roadmap for the team to implement and monitor mitigation strategies.
In a manufacturing facility:
The Mitigation Action Plan Template proves valuable during a quality deviation. The template assists in formulating a structured plan to mitigate the impact on product quality. Immediate corrective actions are outlined, and preventive measures are established to avoid similar deviations in subsequent production cycles. This proactive approach ensures continuous improvement and adherence to quality standards.
Risk Communication Plan
A Risk Communication Plan outlines how risks will be communicated within the organization and to external stakeholders, ensuring transparent and effective communication to mitigate the potential impact of risks.
Example:
In a biopharmaceutical company, the Risk Communication Plan defines protocols for informing regulatory authorities and investors about significant risks, such as unexpected delays in drug development. Clear communication channels and messaging strategies are established to maintain trust and manage expectations.
Imagine a pharmaceutical company introducing a new medication:
The Risk Communication Plan becomes crucial in conveying potential side effects to healthcare providers and patients. By transparently communicating risks and providing clear guidance. The company ensures informed decision-making, fostering trust in the product’s safety and efficacy.
Change Control Risk Assessment Template
The Change Control Risk Assessment Template is designed to assess the potential risks associated with changes in processes, systems, or products, and this template helps evaluate the impact of changes and implement effective risk mitigation measures.
Example:
When implementing a new manufacturing process for a pharmaceutical product. The Change Control Risk Assessment Template is used to evaluate potential risks, such as equipment compatibility and training requirements. The assessment guides the team in implementing changes with minimal disruption and ensures ongoing compliance.
In a fast-paced packaging operation implementing serialization and aggregation system upgrades:
The Change Control Risk Assessment Template is employed. It aids in evaluating the potential risks associated with the changes, such as data migration challenges or temporary service disruptions. The template facilitates a structured approach to assess and address risks, ensuring a seamless transition and minimal impact on operations.
Validation Master Plan (VMP) Risk Section
The VMP includes a dedicated section for assessing and managing risks associated with the validation process.
Example:
In the validation of a new analytical method, the VMP’s risk section is utilized to identify potential challenges. Such as equipment calibration issues. The plan outlines risk mitigation strategies, including regular calibration checks and alternative validation approaches. To ensure the reliability of analytical results.
For a biopharmaceutical firm developing a novel manufacturing process:
The Validation Master Plan’s Risk Section is pivotal. It outlines the risks associated with the validation process, ensuring each step aligns with regulatory standards. By proactively addressing potential pitfalls, the company enhances the likelihood of successful validation, expediting the product’s journey to market.
Audit Trail Review Template
This template facilitates the systematic review of audit trails in regulated environments. Ensuring that electronic records are secure, accurate, and compliant with regulatory requirements.
Example:
In a pharmaceutical manufacturing facility, the Audit Trail Review Template is used to review electronic records of critical processes regularly. This proactive approach helps identify any deviations or anomalies in the audit trail, allowing for immediate corrective actions to maintain data integrity and regulatory compliance.
Conclusion
These examples illustrate how these ten key tools in the Quality Risk Management tools kit can applied in real-world scenarios across the life sciences industry. Each tool plays a crucial role in identifying, assessing, and mitigating risks to ensure the quality, safety, and compliance of products and processes. As organizations continue to navigate complex regulatory landscapes, these tools provide valuable support in fostering a proactive and risk-aware culture.
Download and Read the White Paper
Download this White Paper to unlock success in your life. Science projects by integrating Quality Risk Management (QRM) into Commissioning, Qualification, and Validation (CQV) processes. Discover actionable steps for robust project outcomes and embrace a culture of risk excellence. Learn how PharmAllies can help you achieve your quality and risk management goals today.
Download HERE
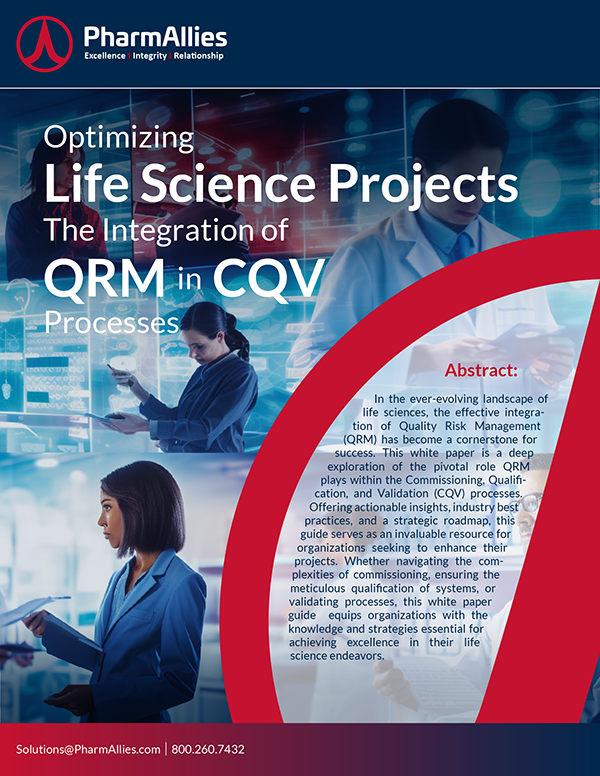
Unlock success in Commissioning, Qualification, and Validation (CQV) projects with our guide. Discover 10 strategic steps for effective Quality Risk Management (QRM).